What does an AGV do in a factory?
Automated guided vehicles (AGVs) are automated robots that transport goods between two points in a warehouse ― or between two connected systems ― without the need for a driver. These vehicles speed up the flow of heavy materials by moving along a pre-designed circuit.
What does AGV stand for in automation?
Sometimes called self-guided vehicles or autonomous guided vehicles, automated guided vehicles (AGVs) are material handling systems or load carriers that travel autonomously throughout a warehouse, distribution center, or manufacturing facility, without an onboard operator or driver.
How does the AGV system work?
A geoguided AGV recognizes its environment to establish its location. Without any infrastructure, the forklift equipped with geoguidance technology detects and identifies columns, racks and walls within the warehouse. Using these fixed references, it can position itself, in real time and determine its route.
What is the difference between AGV and AMR?
The main difference between AMR vs AGV is AMRs can maneuver around obstacles on their own. AGVs must stop until you remove the obstacle. AMRs are like cars and AGVs are like trains – cars can drive around an obstacle, but trains have to stay on the tracks until you remove the obstacle.
What are the benefits of AGVs in warehouse?
With a programmed route and the aid of sensors, the AGV can pick up and offload materials without breaks, slip-ups, or miscalculations. For example, if an AGV is used to transport finished goods from the end of an assembly line and transport them to storage, it can position itself with 100% accuracy every time.
How is AGV used today?
AGVs are often used in the movement of raw materials such as metal, chemicals, plastic or paper within industrial settings. Replacing conveyors, they can facilitate the seamless transfer of these materials from receiving docks to storage areas or directly to production lines.
What is AGV in CNC?
AGV, an automated guided vehicle, and AMR, an autonomous mobile robot, are unmanned transport devices for moving various kinds of loads inside a factory.
How big is the AGV robot market?
The global automated guided vehicle market size was valued at USD 2.12 billion in 2022 and is projected to grow from USD 2.30 billion in 2023 to USD 4.43 billion by 2030, exhibiting a CAGR of 9.8% during the forecast period.
What is the difference between AGV and LGV?
Laser Guided Vehicles (LGVs) are another type of AGV, but differ due to their laser-guided technology. A scanner intercepts the signal emitted by the vehicle and reflected by “mirrors” positioned at strategic points along the route.
What are the applications of AGV in industry?
AGVs excel in enhancing material handling processes within manufacturing facilities by efficiently transporting raw materials, work-in-progress items, and finished goods. Streamlining the movement of materials throughout the manufacturing process, AGVs optimise workflows to drive operational efficiency.
What are the controls for AGV?
The control system is manages the AGV’s actuators, such as motors, brakes, and steering mechanisms, in order to execute the planned motion and ensure the vehicle follows the desired route.
Why are AGVs necessary?
Automated Guided Vehicles (AGVs) are robotic vehicles designed for material handling and transportation within industrial environments. They navigate using sensors and follow predefined routes. AGVs are integral to modern factory automation, enhancing efficiency and safety by streamlining material handling processes.
Which sensor is used in AGV?
LiDAR Sensors LiDAR is a highly capable laser-based sensing system crucial for the navigation and operation of AMRs and AGVs. It helps robots get a detailed 3D picture of their surroundings.
What are the different types of AGV robots?
Three types of AGVs are towing, fork trucks, and heavy load carriers. Each is designed to perform repetitive actions such as delivering raw materials, keep loads stable, and complete simple tasks. Unlike human workers, AGVs operate continuously only needing to stop to be recharged or repaired.
What is AMR in automation?
Autonomous mobile robots (AMRs) use cameras, sensors, artificial intelligence, and machine vision to independently navigate through uncontrolled environments to complete a variety of tasks.
What is an AGV in a factory?
Automated guided vehicle (AGV) are automated material handling solutions that work autonomously, transporting goods and materials through manufacturing facilities, warehouses or distribution centres without a driver or operator.
Why AGVs are valuable in a manufacturing environment?
AGV solutions make movement of equipment and materials more efficient and allow your people to spend more time doing tasks of greater value-add. AGV solutions are ideal when working in tight spaces, or when moving a load through areas with minimal clearance.
How do AGVs navigate?
With line following navigation technologies, AGVs are literally guided through a facility by a physical line, such as magnetic tape, inductive wire (installed in/under the floor) or painted lines. Line following vehicles follow a physical line through a facility.
Why is AGV so expensive?
AGV helmets tend to be more expensive because they are industry-leading. Many of the helmets in AGV’s lineup benefit directly from the extensive research and development carried out to protect Moto GP riders. 1 Why are AGV Helmets So Expensive? 1.1 Can I Find an AGV Helmet Within My Budget?
What motors are used in AGV?
4. Motor Type: The most common motor types for AGVs are DC motors and brushless DC (BLDC) motors. DC motors are cost-effective and straightforward, while BLDC motors offer better efficiency, longer life, and smoother operation.
How are AGVs used today?
AGVs are currently being used in a wide range of applications, like transporting raw materials that include (but are not limited to) metal, paper, plastic, and rubber. One example of this is the transporting of raw materials from a receiving dock to a warehouse or even directly to the production line.
What is AGV used for material handling?
An automated guided vehicle (AGV) system transports various goods via computer-driven vehicles from a pick location to a drop location. The fleet manager distributes single transport orders to the vehicles. The shortest path to the destination is then calculated by the fleet manager.
How does and AGV safety system work?
Safety sensors have multiple safety fields. The main fields are stop field and slow down field. Within the slow down field the AGV reduces speed and in the stop field the AGV immediately stops. The fields are configured by speed and steering angle.
What is the cost of AGV robot?
Automated Guided Vehicle, Lifting Capacity: 2,000 lbs at Rs 1500000 in Mumbai.
Who made AGV?
Founded in 1947 by Gino Amisano (1920–2009), AGV rapidly won an unrivalled reputation for its innovative designs and materials, tested on the racetrack and developed with sponsored World Championship riders, including 15-times World Champion Giacomo Agostini and modern MotoGP legend Valentino Rossi.
What is the role of robots in a motor vehicle assembling plant?
ROBOTIC ASSEMBLY – Tasks such as screw driving, windshield installation and wheel mounting are all candidates for robotic arms in car manufacturing plants. In many automotive part plants, robots — for example, the high-speed “Delta” machines — are assembling smaller component assemblies such as pumps and motors.
What is AGV used for material handling?
An automated guided vehicle (AGV) system transports various goods via computer-driven vehicles from a pick location to a drop location. The fleet manager distributes single transport orders to the vehicles. The shortest path to the destination is then calculated by the fleet manager.
Why are AGVs necessary?
Automated Guided Vehicles (AGVs) are robotic vehicles designed for material handling and transportation within industrial environments. They navigate using sensors and follow predefined routes. AGVs are integral to modern factory automation, enhancing efficiency and safety by streamlining material handling processes.
What are autonomous mobile robots used for?
Retailers, banks, and hospitality companies are using AMRs to streamline and enhance the customer experience—from customer service to inventory automation, room service, luggage assistance, and way finding.
What is an automated guided vehicle (AGV) system?
What are AGV vehicles?
What is an AGV system?
When were AGVs invented?
What are AGVs assembly line vehicles?
What is a laser guided vehicle (AGV)?
Okay, so you’ve heard the buzz about AGV factory automation, but you’re not sure what it is or if it’s right for your business. Don’t worry, you’re not alone! We’re here to break it down, starting with the basics.
AGV stands for Automated Guided Vehicle. Think of it as a robot on wheels that can move materials around your factory floor. They’re not new technology, but they’re becoming more sophisticated and affordable.
Why are AGVs so popular? They offer a bunch of benefits:
Increased efficiency: Imagine your factory running smoothly, with materials delivered exactly when and where they’re needed. That’s the power of AGVs! They streamline your processes and reduce downtime.
Improved safety: AGVs take over the dangerous and repetitive tasks, reducing the risk of accidents for your human workforce.
Reduced costs: By automating material handling, you can cut down on labor costs and improve overall productivity.
Flexibility: AGVs can be easily reprogrammed to adapt to changes in your production processes.
But how do they actually work?
AGVs rely on a variety of navigation technologies, like:
Laser guidance: This is the most common method. AGVs use lasers to scan reflective markers on the floor, creating a map of their environment.
Magnetic tape guidance: This system uses magnetic strips embedded in the floor to guide the AGVs.
Vision-based navigation: AGVs with cameras can recognize landmarks and navigate based on visual information.
Natural navigation: The latest AGVs can even use sensors to “learn” the environment and navigate without needing any physical guidance.
Choosing the right AGV for your needs
Now, you can’t just go and pick any AGV off the shelf. There are tons of options, and choosing the right one depends on your specific requirements:
Payload capacity: How much weight will your AGV need to carry?
Speed: How quickly does your material need to be moved?
Navigation technology: What type of navigation system is best suited for your factory environment?
Safety features: Make sure your AGV comes equipped with the necessary safety features to keep your workers safe.
Integrating AGVs into your factory
Once you’ve chosen the right AGVs, you need to think about integrating them into your existing systems. This might involve:
Modifying your factory layout: Make sure you have enough space and clear paths for your AGVs to navigate.
Connecting to your existing IT systems: You’ll need to connect your AGVs to your ERP and other systems to track materials and manage production.
Training your workforce: Your employees will need to learn how to operate and maintain the AGVs.
The benefits of AGV factory automation
We’ve talked about the general benefits of AGVs, but let’s dive a little deeper:
Reduced lead times: By speeding up material handling, you can get products to market faster.
Increased production output: With faster and more efficient material flow, you can increase your overall production output.
Improved product quality: Accurate and consistent material handling leads to less variability in your products.
Enhanced workplace safety: By removing hazardous tasks from human workers, you create a safer working environment.
Examples of AGVs in action
AGVs are used in a wide range of industries:
Automotive: Transporting car parts, finished vehicles, and materials around assembly plants.
Electronics: Moving components, printed circuit boards, and finished products through manufacturing lines.
Food and beverage: Handling ingredients, packaging materials, and finished products in food processing facilities.
Pharmaceuticals: Transporting raw materials, chemicals, and finished medicines in pharmaceutical production lines.
Are you ready to take the leap?
If you’re thinking about incorporating AGVs into your factory, here are a few things to consider:
Cost: AGVs can be a significant investment, but they can also lead to long-term cost savings.
Return on investment: Make sure you understand the potential ROI before you invest in AGVs.
Maintenance: AGVs require regular maintenance to keep them running smoothly.
Safety: Thorough safety training and procedures are essential for operating AGVs safely.
FAQs about AGV factory automation
1. What are the different types of AGVs?
AGVs come in a variety of shapes and sizes, depending on their application. Common types include:
Forklift AGVs: These AGVs are designed to lift and transport pallets.
Towing AGVs: These AGVs are used to tow trailers or carts.
Unit load AGVs: These AGVs are designed to transport individual items or units.
2. How much do AGVs cost?
The cost of an AGV depends on several factors, including payload capacity, navigation technology, and safety features. Prices can range from a few thousand dollars to hundreds of thousands of dollars.
3. How do I know if AGVs are right for my factory?
Consider the following factors:
The size and layout of your factory: AGVs need enough space to navigate.
The volume of materials you need to move: AGVs are ideal for high-volume material handling.
The types of materials you need to move: Choose an AGV with the right payload capacity and handling capabilities.
4. What are the safety considerations for AGVs?
Safety is paramount when it comes to AGVs. Here are some key considerations:
Collision avoidance: AGVs are equipped with sensors to detect obstacles and prevent collisions.
Emergency stops: AGVs should have emergency stop buttons and other safety features.
Operator training: Your employees need to be properly trained on how to operate and interact with AGVs safely.
5. How do I get started with AGV factory automation?
Start by assessing your needs: Determine which areas of your factory could benefit from AGV automation.
Research different AGV providers: Compare features, prices, and customer support.
Get a pilot project underway: Start with a small-scale project to test the technology and see how it works in your environment.
Partner with an experienced integrator: A professional integrator can help you choose the right AGVs and integrate them into your factory.
Conclusion
AGV factory automation is rapidly transforming the manufacturing industry. By embracing this technology, you can improve efficiency, reduce costs, and enhance safety. As you’ve learned, there’s a lot to consider when implementing AGVs, but with careful planning and execution, you can reap the rewards of this exciting technology.
See more here: How Does The Agv System Work? | Agv Factory Automation
Automated Guided Vehicles – AGV Systems | Dematic
Automated Guided Vehicles (AGVs) transport and store a wide range of products and materials in a variety of industries and operations — factories, warehouses, distribution Dematic
Automated Guided Vehicle | AMS, Inc
A true cornerstone in factory automation. The AGV is the essential magnetic guided vehicle that can be customized to your specifications. Maximize your workflow with AMS’ AMS, Inc
Automated Guided Vehicles (AGV) | Meaning, Types & Use-Cases
An Automated Guided Vehicle (AGV) system, also referred to as autonomous guided vehicles, self-guided vehicles or mobile robots, are material handling systems that AutoStore
Automated guided vehicles – AGV platforms | Stäubli – staubli.com
Stäubli designs and manufactures premium AGV (Automated Guided Vehicle) solutions. Over the last 20 years, our AGV platforms series have delivered agile motion on the Stäubli
Automated guided vehicle systems | KUKA AG
KUKA develops and integrates automated guided vehicle systems (AGVS) for barrier-free, versatile and flexibly expandable networking of your production and warehouse logistics. KUKA AG
Guiding the Industry: AGVs and the Smart Factory
In industry, automated guided vehicles (AGVs) use environmental stimuli to follow a specific route. This article discusses how automated guided vehicles have Automation.com
Autonomous Guided Vehicles for Smart Industries
Autonomous Guided Vehicles (AGVs) are considered to be one of the critical enabling technologies for smart manufacturing. This paper focus on the application of Springer
Automated Guided Vehicles | Kollmorgen
With our NDC Solutions automation kit consisting of hardware, software and navigation technologies you get a proven platform for boosting AGV performance in a broad range Kollmorgen
What Are Automated Guided Vehicles (AGVs)? | Spectra
What Is an Automated Guided Vehicle System? Automated guided vehicles (AGVs) are materials-handling machines that are autonomous and driverless. Spectra by Mitsubishi Heavy Industries Group
See more new information: v1.vietmasks.com
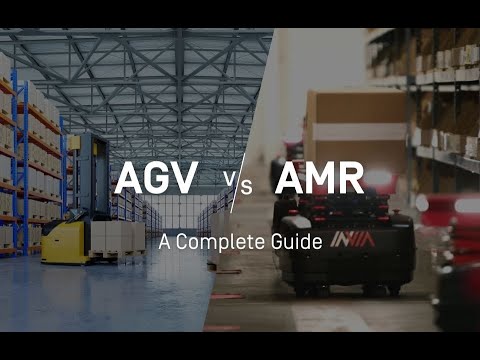
Link to this article: agv factory automation.
See more articles in the same category here: https://v1.vietmasks.com/category/automation-technology blog