What is a control system in industrial automation?
Industrial automation control systems involve the integration of devices, machines, and equipment within the manufacturing plant. As mentioned above, however, they can also go further than this by integrating the system on the plant floor with the rest of the organisation.
Which controller is used in industries?
A proportional-integral-derivative (PID) controller is a control mechanism that is widely used in various industrial applications. The controller’s purpose is to regulate a system’s output by adjusting its input, taking into account the system’s error, rate of change, and accumulated error.
What are the different types of industrial automation?
Industrial processes can be controlled manually, but with industrial automation, machines can be controlled through the use of computers and other electronic devices. There are four main types of industrial automation: fixed automation, programmable automation, flexible automation, and integrated automation.
How many types of controllers are there?
There are three basic types of controllers: on-off, proportional and PID. Depending upon the system to be controlled, the operator will be able to use one type or another to control the process.
What are the 3 types of control system in automation?
There are three types of controllers used in industrial automation: Programmable Logic Controllers(PLCs), Distributed Control System(DCSs), and Programmable Automation Controller (PACs).
What are the three types of industrial control system?
a general term that encompasses several types of control systems, including supervisory control and data acquisition (SCADA) systems, distributed control systems (DCS), and other control system configurations such as Programmable Logic Controllers (PLC) often found in the industrial sectors and critical infrastructures …
Which type of control system is commonly used in industrial applications?
Programmable Logic Controllers (PLCs): PLCs serve as the brain of many industrial control systems. They process information from sensors and issue commands to actuators. The hardware configuration of PLCs includes a central processing unit (CPU), input and output modules, and communication interfaces.
What is the most commonly used controller?
Overview. Proportional-Integral-Derivative (PID) control is the most common control algorithm used in industry and has been universally accepted in industrial control.
Why controllers are used in industry?
They are used in many industries to monitor and control production processes and building systems. Once programmed, the PLC will perform a sequence of events triggered by stimuli referred to as inputs. It receives these stimuli through delayed actions such as counted occurrences or time delays.
What is the difference between PLC and industrial controller?
Industrial PCs can perform the same tasks as PLCs but with an operating system that enables them to run various applications and programs that are not available for PLCs. With these capabilities, IPCs are more than just control purposes. Industrial PCs can consolidate workloads which reduces hardware footprint.
What are the four 4 types of automation?
Let’s take a closer look at the four primary types of automation: programmable, fixed, flexible, and integrated. Picture a bustling factory floor, where robots move with precision and efficiency, assembling products seamlessly. This scene is a testament to programmable automation’s power.
What is used in industrial automation?
Industrial automation is the use of control systems, such as computers or robots, and information technologies for handling different processes and machineries in an industry to replace a human being. It is the second step beyond mechanization in the scope of industrialization.
What are the different types of controller inputs?
There are three main types of gaming controller inputs: standard push buttons, pressure sensitive buttons, and analog sticks. Each type of input requires unique circuitry to be measured and transmitted accurately. Unlike push buttons, pressure sensitive buttons are analog inputs.
How are controllers classified?
There are two main types of controllers: continuous controllers, and discontinuous controllers. In discontinuous controllers, the manipulated variable changes between discrete values.
What is an automation controller?
Automation controller is the central location to configure and manage how automation runs across your infrastructure.
What are controllers in engineering?
A controller is the most important component of the control system. It is responsible for the performance of the control system. It is a device or an algorithm that works to maintain the value of the controlled variable at set point.
What is the difference between a controller and an actuator?
Controller controls the system by introducing changes in its variable(s) so that the system produces desired output. Actuator is a device that implements the changes that controller introduces into the system. Thanks for the question.
What are the different types of controllers in a control system?
The document discusses proportional (P), integral (I), and derivative (D) controllers which are commonly used in closed-loop control systems. It provides examples of how each controller type affects characteristics like rise time, overshoot, settling time, and steady-state error.
What are the types of automated control?
Automated controls rely on computerized (electronic) actions. For instance: Authentication measures are put in place to authorize access to a system or process a transaction. Edit functions can ensure data accuracy and completeness.
What are the three types of automation systems?
Three types of automation in production can be distinguished: (1) fixed automation, (2) programmable automation, and (3) flexible automation.
What are the controllers used in industry?
Programmable Logic Controller (PLC) This is a type of hardware that is used in both DCS and SCADA systems as a control component of an overall system. It also provides local management of processes being run through feedback control devices such as sensors and actuators.
What is control in industrial automation?
Industrial control system (ICS) is a collective term used to describe different types of control systems and associated instrumentation, which include the devices, systems, networks, and controls used to operate and/or automate industrial processes.
What are the three types of control systems?
Organizational control systems allow executives to track how well the organization is performing, identify areas of concern, and then take action to address the concerns. Three basic types of control systems are available to executives: (1) output control, (2) behavioral control, and (3) clan control.
What are PLC used to control?
A programmable logic controller (PLC) or programmable controller is an industrial computer that has been ruggedized and adapted for the control of manufacturing processes, such as assembly lines, machines, robotic devices, or any activity that requires high reliability, ease of programming, and process fault diagnosis.
What are the three types of controls in PLC?
PLC are divided into three types based on output namely Relay output, Transistor output, and Triac Output PLC. The relay output type is best suited for both AC and DC output devices.
What is control system in PLC?
A programmable logic controller is a type of tiny computer that can receive data through its inputs and send operating instructions through its outputs. Fundamentally, a PLC’s job is to control a system’s functions using the internal logic programmed into it.
What are controllers used for?
The importance of controllers Controllers and drivers provide important links between the computer and devices and applications being used. While the OS controls computer functions, controllers and their associated drivers extend OS functionality to specialized tools and resources that increase a user’s productivity.
What are the different types of controllers used in industrial automation?
What are the different types of automation control systems?
What are the different types of industrial control systems?
What are the 3 main automated control systems?
What are the three types of control systems?
What are automation control systems?
Let’s dive into the fascinating world of industrial automation controllers. These are the brains behind the operation of automated systems in factories, power plants, and other industrial settings. Think of them as the decision-makers, orchestrating the intricate dance of machines and processes.
PLC (Programmable Logic Controller)
Imagine a super-smart switchboard that can be programmed to control and monitor a wide range of industrial processes. That’s the essence of a PLC. It’s the workhorse of automation, handling everything from simple tasks like turning a motor on and off to complex sequences involving multiple machines.
What makes a PLC so special?
Robustness: PLCs are built to withstand harsh industrial environments, withstanding vibrations, temperature fluctuations, and electrical noise.
Flexibility: You can easily reprogram a PLC to adapt to changes in your production line or process.
Reliability: PLCs are designed for continuous operation and are known for their high uptime, minimizing downtime and maximizing productivity.
Connectivity: Modern PLCs are equipped with networking capabilities, allowing them to communicate with other devices and systems.
Typical applications:
Conveyor systems: Managing the movement of products along a conveyor belt.
Packaging machines: Controlling the filling, sealing, and labeling of products.
Robotics: Coordinating the movements of robotic arms in assembly tasks.
Process control: Monitoring and regulating variables like temperature, pressure, and flow in chemical and manufacturing processes.
PAC (Programmable Automation Controller)
While PLCs are great for controlling discrete tasks, PACs are more suited for managing complex, continuous processes. Think of them as the more sophisticated and versatile cousins of PLCs.
What sets a PAC apart?
Open architecture: PACs are designed with an open architecture, allowing them to integrate with different devices and software from various vendors.
Advanced functionality: They offer more powerful processing capabilities, supporting complex algorithms, real-time data analysis, and advanced control techniques.
Real-time control: PACs are often used in applications requiring real-time data acquisition and control, like in process industries.
Integration with IT systems: They seamlessly integrate with enterprise resource planning (ERP) systems and other business software, enhancing data management and decision-making.
Common uses:
Process automation: Optimizing and controlling continuous processes in industries like pharmaceuticals, chemicals, and power generation.
Motion control: Managing complex movements in machines like robots, CNC machines, and automated guided vehicles.
Data acquisition and analysis: Collecting and analyzing real-time data from sensors and actuators, providing insights for process optimization.
CNC (Computer Numerical Control)
Ever wondered how those intricate shapes and patterns are created on metal parts? CNCs are the machines that make it possible. They are essentially computer-controlled machines that use numerical instructions to guide tools, allowing for precise and repeatable machining operations.
Here’s how CNCs work their magic:
Numerical instructions: The CNC machine receives a program of numerical instructions, often stored in a G-code file, which defines the path of the cutting tool.
Precise movements: The CNC machine uses servomotors and other precision mechanisms to accurately control the movement of the cutting tool, ensuring the desired shape and dimensions are achieved.
Automation: CNC machines automate the machining process, reducing the need for manual intervention and improving accuracy and consistency.
CNCs find their niche in industries like:
Automotive manufacturing: Producing engine blocks, chassis parts, and other components.
Aerospace manufacturing: Creating complex parts for aircraft and spacecraft.
Tool and die making: Manufacturing molds and dies for plastic injection molding and other processes.
Woodworking: Producing intricate designs and patterns on furniture and other wood products.
DCS (Distributed Control System)
Imagine a vast network of controllers scattered across a large-scale process plant, working together to manage and optimize the entire operation. That’s the power of a DCS. It’s designed to control and monitor complex and geographically dispersed industrial processes.
What makes a DCS a game-changer?
Centralized control: A DCS provides a central control room for operators to monitor and manage multiple processes simultaneously.
Redundancy: DCSs are designed with redundancy, ensuring that if one controller fails, another takes over to maintain system operation.
Scalability: They are highly scalable, enabling you to easily add or remove controllers as your operation grows or changes.
Advanced control algorithms: DCSs can implement sophisticated control algorithms to optimize processes and improve efficiency.
Where DCS shines:
Power plants: Controlling steam generation, power distribution, and other critical operations.
Oil and gas refineries: Managing complex chemical processes and ensuring safe and efficient operation.
Water and wastewater treatment: Controlling water purification and waste treatment processes.
Large-scale manufacturing: Coordinating and managing production lines across multiple facilities.
SCADA (Supervisory Control and Data Acquisition)
Think of a system that acts as the eyes and ears of your industrial process, collecting data, monitoring operations, and providing real-time insights. That’s SCADA in a nutshell. It’s a powerful tool for visualizing, analyzing, and optimizing industrial processes.
SCADA’s key characteristics:
Data acquisition: SCADA systems collect data from various sources, including sensors, actuators, and other devices in the process.
Visualization: They provide real-time visualization of process data, enabling operators to monitor and understand the status of the system.
Control and alarm management: SCADA systems can trigger alarms based on predefined conditions and provide control functionalities for responding to events.
Data analysis and reporting: They offer data analysis tools to identify trends, patterns, and potential issues, helping to optimize process performance.
SCADA is vital for:
Power distribution: Supervising power generation, transmission, and distribution networks.
Oil and gas pipelines: Monitoring the flow of oil and gas through pipelines and detecting leaks or other issues.
Transportation systems: Controlling traffic signals, monitoring train operations, and managing airport systems.
Water and wastewater treatment: Supervising water purification and treatment plants.
Choosing the Right Controller for Your Application
With so many options, selecting the right controller for your application can be challenging. Here’s a guide to help you make an informed decision:
Complexity of the process: For simple, discrete tasks, a PLC may be sufficient. However, for complex, continuous processes, a PAC or DCS might be more suitable.
Size and scale of the operation: Small-scale operations may be adequately served by a PLC or a single PAC, while large-scale facilities may require a DCS.
Environmental conditions: PLCs are generally robust and well-suited for harsh industrial environments.
Budget: Controllers vary in price, with PLCs typically being more affordable than PACs and DCSs.
Let’s summarize:
| Controller Type | Applications | Key Features |
|—|—|—|
| PLC | Discrete tasks, simple control | Robust, reliable, flexible |
| PAC | Complex processes, advanced control | Open architecture, real-time control, integration with IT systems |
| CNC | Precision machining | Computerized control, numerical instructions |
| DCS | Large-scale, distributed processes | Centralized control, redundancy, scalability |
| SCADA | Data acquisition, visualization, and optimization | Data collection, real-time monitoring, alarm management |
FAQs:
Q: What are the differences between a PLC and a PAC?
A: A PLC is typically used for discrete tasks and control, while a PAC is designed for more complex, continuous processes. PACs offer advanced functionality, open architecture, and seamless integration with IT systems.
Q: Which type of controller is best for a small manufacturing plant?
A: A PLC is generally a good choice for a small manufacturing plant, as it is robust, reliable, and affordable.
Q: What is the role of a human operator in a system controlled by a PLC or PAC?
A: While PLCs and PACs automate tasks, human operators play a crucial role in monitoring the system, making adjustments, troubleshooting problems, and ensuring safety.
Q: How do I choose the right controller for my specific application?
A: Consider the complexity of your process, the size and scale of your operation, the environmental conditions, and your budget when making your decision.
Q: What are some common programming languages used for PLCs and PACs?
A: Common programming languages for PLCs and PACs include ladder logic, function block diagrams, and structured text.
Q: What are the benefits of using industrial controllers in automation?
A: Industrial controllers offer numerous benefits, including improved efficiency, accuracy, consistency, and safety in automated processes.
Q: How do I learn more about industrial automation and controllers?
A: There are many resources available online and in libraries, including textbooks, articles, and online courses.
Ready to dive deeper into the exciting world of industrial automation? There are many more aspects to explore, including programming languages, communication protocols, and security considerations. Keep learning, keep experimenting, and keep automating!
See more here: Which Controller Is Used In Industries? | What Are The Different Types Of Controllers Used In Industrial Automation?
What Are The 3 Types Of Control Systems In Automation?
Three main types of automated control systems are Programmable logic controllers, distributed control systems, and programmable automation control Automation Electric & Controls
What Are The Different Types Of Industrial
Programmable logic controllers, otherwise known as PLCs, are industrial computers, specifically designed for the harsh manufacturing environment. A PLC receives an input of data. Then its outputs contain Automation Electric & Controls
Programmable Logic Controllers (PLCs): Basics,
Types of PLCs: There are compact and modular PLCs, with modular versions allowing for expanded control options and adaptability. Industrial Applications: Programmable logic controllers are crucial in Electrical4U
Types of Industrial Control Systems – Thomasnet
Industrial Control System (ICS) is a collective term used to describe different types of control systems and related instrumentation, which include the devices, Thomasnet
The Complete Guide to Industrial Automation – Clarify
Programmable logic controllers or just programmable controllers are modular industrial computers used for the control of various automated processes, Clarify
How to choose an industrial automation controller
The controller specified, such as a programmable logic controller (PLC) or programmable automation controller (PAC), can control a single station, a machine, a Control Engineering
Automation Controllers – PROFINET University
There are three types of controllers used in industrial automation: Programmable Logic Controllers (PLCs), Distributed Control System (DCSs), and Programmable PROFINET University
See more new information: v1.vietmasks.com
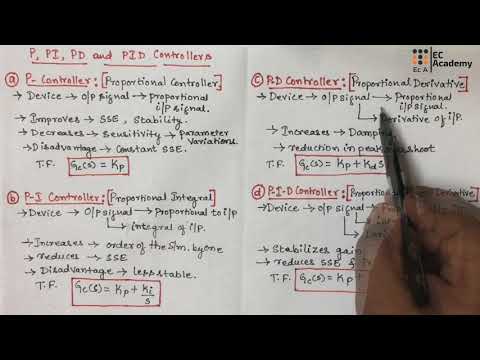
Link to this article: What are the different types of controllers used in industrial automation?.
See more articles in the same category here: v1.vietmasks.com/category/automation-technology